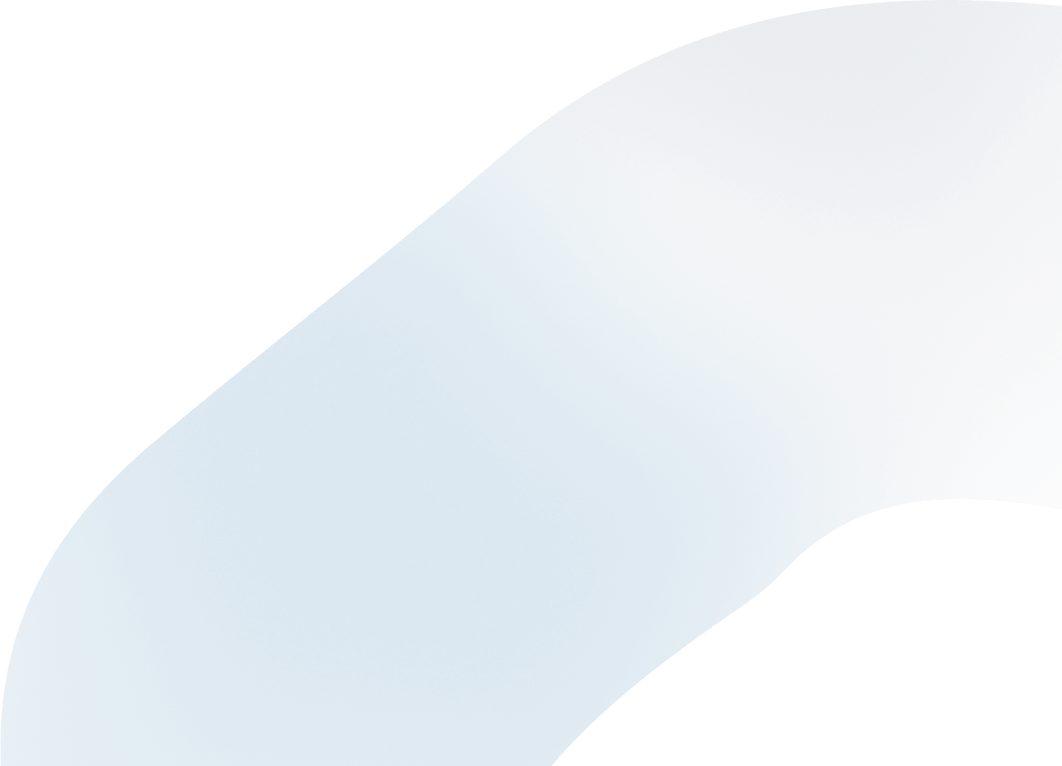
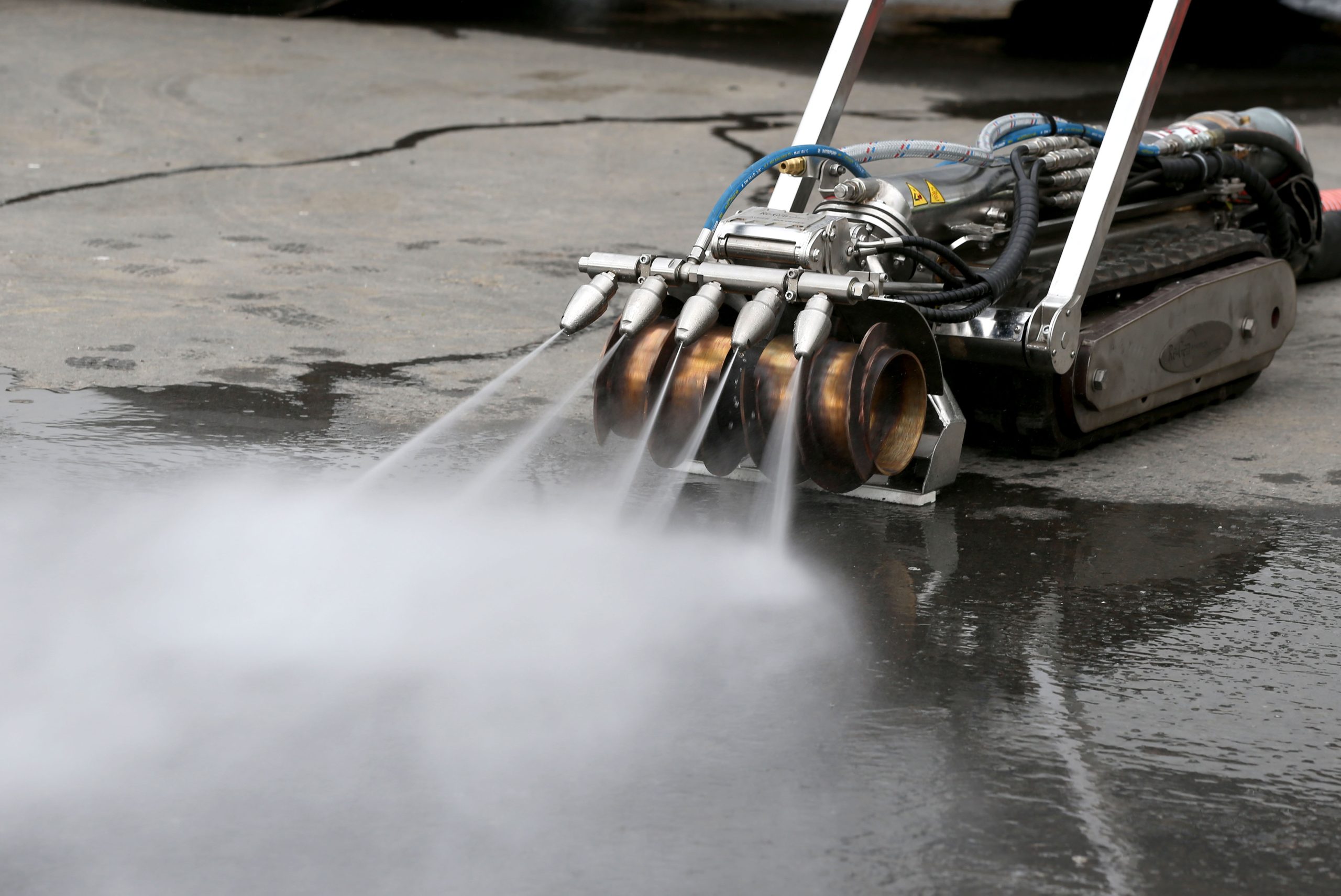
Re-Gen Robotics’ Commercial Director, Chris Platt, explains how their unique cleaning services incorporating patented proven robotic tank cleaning technology can help you complete routine tasks in new and safer way.
Storage tanks must be emptied and cleaned on a regular basis. Especially when this involves removing oils at the heavier end of the crude oil barrel, noxious, semi-solid sludges on occasion containing scale or catalyst fines present considerable challenges to those trying to remove them from tanks.
Historically, the industry has resorted to sending teams of personnel, wearing all enveloping plastic suits and breathing apparatus into these tanks to shovel the sludge out, manually. Such activity entails lengthy and expensive procedures to keep the entrants safe. During sludge removal, operatives are at risk from the flammable and toxic hazards of the materials they are having to deal with. Modern technology has meant that in most circumstances, humans can be replaced by Zone 0 Ex certified robots.
Recently, when one of Re-Gen Robotics’ clients was faced with what turned out to be 2000 tonnes of sludge for removal from a tank, they called Re-Gen Robotics. They knew that we had experience working with heavy oils which resisted others’ attempts to remove them safely. They stated their desire to avoid manned entry if possible and elected to isolate the human from the hazards within the tank.
Below is the story of that job…
Planning
Our extensive planning process, based on site plot plans and tank drawings assessed manway availability of 24” (600mm) diameter. Then we reviewed siting possibilities for our kit, as per zoning requirements, together with options for human and vehicle access routes. Next, we developed our intended robot travel plan within the tank, taking into account heating coils and roof water drains.
Pumpdown
As the level of sludge within the tank was above the manways, our first task was to assist the client to remove sludge to below manway level. This was accomplished using progressive cavity pumps and hose access gained at mixer flanges.
Sludge removal
During this phase of the job, the majority of material within the tank was removed. Heat was added to the oil to reduce its viscosity and the material was kept warm throughout its processing. It was removed to the site’s waste facility for further processing and eventual disposal of residual solids and non-recyclable material.
Robot Wash
Achieving a higher standard of cleanliness, especially around internal furniture and on walls was completed using different suction and jetting heads.
Finishing to hot work standards
Finally, once only the last residues of oil were present and the sludge had been removed final mopping and drying was carried out.